
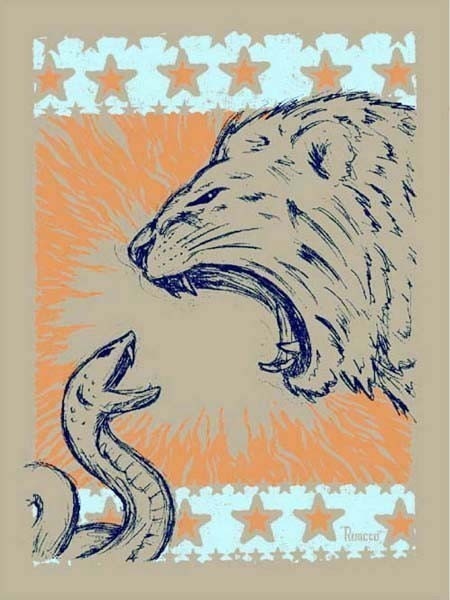
This technique is best used to obtain the multi-colour printing look without actually doing it. The entire process uses a single colour of ink, and this colour gets half-toned, resulting in a different shade when looked at from a distance. In halftone printing, single colours in gradients are printed. It can be an excellent option for printing on t-shirts, jackets, and hoodies, for example. It is much simpler to use as compared to other screen printing methods. This technique produces a vibrant solid spot of colour. Spot colour screen printing uses the ink's stock colour by printing it through the stencil of the mesh. The most common screen printing technique is spot colour screen printing. Since different techniques will provide different results, it is important to understand the different types. There are six different types of screen printing processes. This is done so that the design does not fade away.
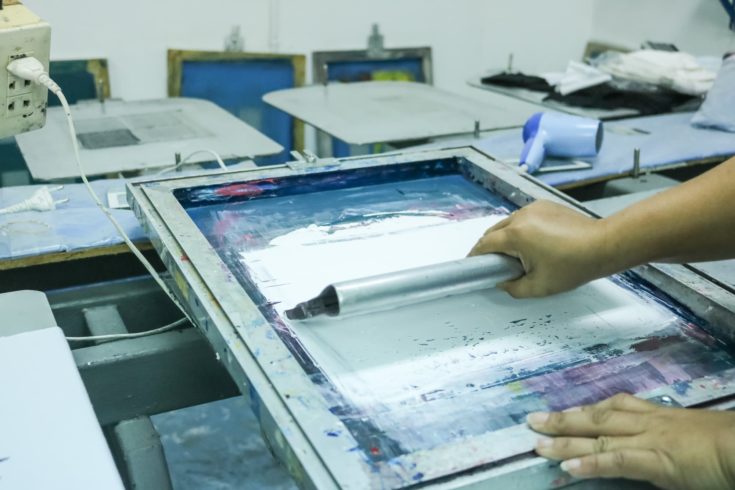
Lastly, the printed product is heat-cured by passing through a dryer, creating a smooth design. The material to be printed is placed flat on the printing board, and the screen on top of the material in the desired position, ready to be printed. The screen is then dried, and if there are any touch-ups required, it will be done by the printer to make the imprint as close to the original design as possible. Stencil CreationĮxposing the screen for a specific time will harden the uncovered areas of the screen, and the remaining unhardened emulsion, if any, will be rinsed away to leave a clear imprint on the screen. It must be noted that when multiple colours are involved in the design, separate screens must be used for different colours. The transparent acetate film is placed on the emulsion-coated mesh screen carefully under a bright light which causes the emulsion to harden and develop. Dual-cure emulsions : Combination of Diazo and SBQ, requires mixing, overall cure time is less than Diazo, price is lower than SBQ.SBQ-based : No mixing needed, cures extremely quickly, expensive, suitable for detailed work.Diazo : Cheaper, needs a longer exposure, not suitable for detailed prints.Generally, there are three main types of emulsion: Screens with a low mesh count let the ink flow through due to wider openingsĪfter the mesh screen is selected, it is coated with a light-reactive emulsion layer.A higher mesh count can print finer details while preserving a fair coating of ink.Which mesh count you need will depend on the design being printed: Mesh count is the total number of fibres in one square inch. When the design is all set to go, it is time to select the screen and mesh count. Once a design has been decided upon, it is printed onto a transparent acetate film, which will then be used to create the screen or stencil. The first step in the process of screen printing is to create the design. Below is the screen printing process step by step: Step 1. The differences can be of the type of ink used, its rendered effect and the printed surface. Screen printing can be done by hand or using a machine but the basic process is always the same. It is a very popular technique because of many reasons, but the most compelling reason is the vast choice of colours that can be used. The most common surface used in screen printing is paper and fabric, but metal, wood, and plastic can also be used. The basic process of screen printing involves creating a stencil on a mesh screen and then pushing the ink to create and imprint the design on the below surface. Screen printing, also known as silk screening or silkscreen printing, is the process of transferring a stencilled design onto a surface using a mesh screen, ink, and a squeegee (a rubber blade). In this article, we will discuss the screen printing process, its uses, types, and benefits. One of the biggest advantages of screen printing is that it can print on almost any kind of surface, be it fabric, paper, glass, wood, card, plastic or leather.
#Silkscreen vs screenprint manual
While screen printing can be manual - especially used when there are only small print runs required - it is very often automated, using advanced inks and materials in combination with computer technology to mass print.
